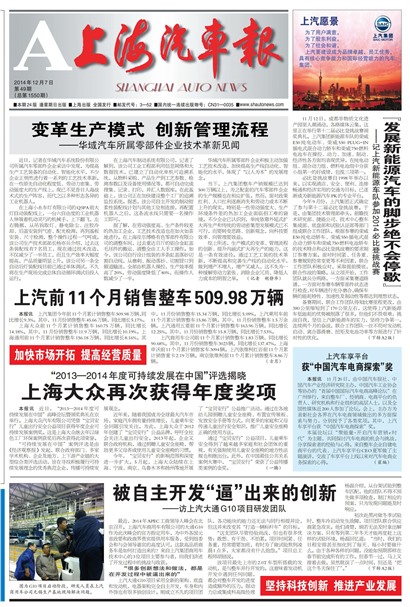
闂傚倸鍊搁崐鎼佸磹瀹勬噴褰掑炊瑜忛弳锕傛煕椤垵浜濋柛娆忕箻閺屸剝寰勭€n亝顔呭┑鐐叉▕娴滃爼寮崶顒佺厪闊洦娲栧暩闂佸憡绻冮〃濠傤潖缂佹ḿ鐟归柛銉戝喚娼婚梻浣告啞椤ㄥ棗煤濡警鍤楅柛鏇ㄥ灠缁犳稒銇勯幒鍡椾壕缂備焦鍔栭惄顖氼潖濞差亜浼犻柛鏇炵仛鏁堥梻浣规偠閸斿矂濡堕幖浣哄祦婵°倕鎳庨崡鎶芥煏韫囧﹥顎嗛柟閿嬫そ閺岋綁鎮╅崗鍛板焻闂佸憡鏌ㄩ懟顖炲煝瀹ュ绠涢柣妤€鐗忛崢鐢告⒑閸涘﹤鐏熼柛濠冪墱閳ь剚鐔幏锟�53BK闂傚倸鍊搁崐鎼佸磹閹间礁纾圭€瑰嫭鍣磋ぐ鎺戠倞鐟滄粌霉閺嶎厽鐓忓┑鐐靛亾濞呭棝鏌涙繝鍌涘仴闁哄被鍔戝鏉懳旈埀顒佺閹屾富闁靛牆楠搁獮鏍煟韫囨梻绠為柨婵堝仜楗即宕煎┑鍫濆Е婵$偑鍊栫敮鎺斺偓姘煎墰缁寮介‖顒佹閺佸倻绮电€n亜濡兼繝纰樻閸ㄦ壆鈧凹鍓濋悘鍐⒑缂佹﹫鑰挎繛浣冲嫮顩锋繝濠傜墛閳锋垿鎮介锝呮灓缂佸顕ц彁闁搞儜宥堝惈闂佽鍠楃划鎾诲箰婵犲啰鐝堕柍鐟扮仢婵倿鏌$仦鐐缂佹梻鍠栭、娑橆潩椤戣棄浜惧┑鐘宠壘缁犳澘顭跨捄铏圭伇缁惧彞绮欓弻娑氫沪閹规劕顥濋梺閫炲苯澧存い銉︽尭閳诲酣濮€閵堝棙娅㈤梺缁樕戣ぐ鍐倵椤撱垺鈷掗柛灞炬皑婢ф稓绱掔€n偅宕岀€殿喗濞婇弫鍐磼濞戞艾骞楅梻渚€娼х换鍫ュ磹閺嵮€妲堢憸鏃堝蓟濞戙垹惟闁挎柨澧介悾鑲╃磽娴d粙鍝洪悽顖ょ節瀵偄顓兼径濠勵槹濡炪倖鍔х紞鍡涘船椤撱垺鈷掗柛灞捐壘閳ь剚鎮傚畷鎰槹鎼达絿鐒兼繛鎾村焹閸嬫挻顨ラ悙瀵稿⒌妞ゃ垺娲熸俊鍫曞磼濮橆偄顥氭繝娈垮枟閿氱€规洦鍓熷畷銏⑩偓鐢电《閸嬫挾鎲撮崟顒傤槷濡炪値鍋勯ˇ閬嶅焵椤掑嫭娑ч柕鍫⑶归锝夊醇閺囩偟顓洪梺缁樏悘姘掓惔銏㈢瘈闁汇垽娼ф禒鈺呮煙濞茶绨界€垫澘锕幊鐐哄Ψ瑜忚ぐ鐐節閻㈤潧孝闁稿﹤顕槐鎾愁潩椤戠偛缍婇幃鈩冩償閿濆棙鍠栭梻浣虹帛閹稿爼宕曢懠顒佸床婵犻潧顑嗛ˉ鍫熺箾閹寸偟鎳愭俊顐磿缁辨挻鎷呴幓鎺嶅闁诲骸鍘滈崑鎾绘煕閺囥劌澧伴柛妯绘崌閹嘲饪伴崟顓犵厜閻庤娲樼划宀勶綖濠靛鍤嬮柛顭戝亝閻濇牠姊绘笟鈧ḿ褏鎹㈤崼銉ョ9闁哄洢鍨归崙鐘裁归敐鍫涒偓鈧柛瀣崌閻涱噣宕归鐓庮潛婵$偑鍊х紓姘跺础閸愬樊鍤曢柡灞诲劚缁犵懓霉閿濆懏璐¢柛娆忔濮婅櫣绱掑Ο鑽ゎ槬闂佺ǹ锕ゅ﹢閬嶅焵椤掍胶鍟查柟鍑ゆ嫹